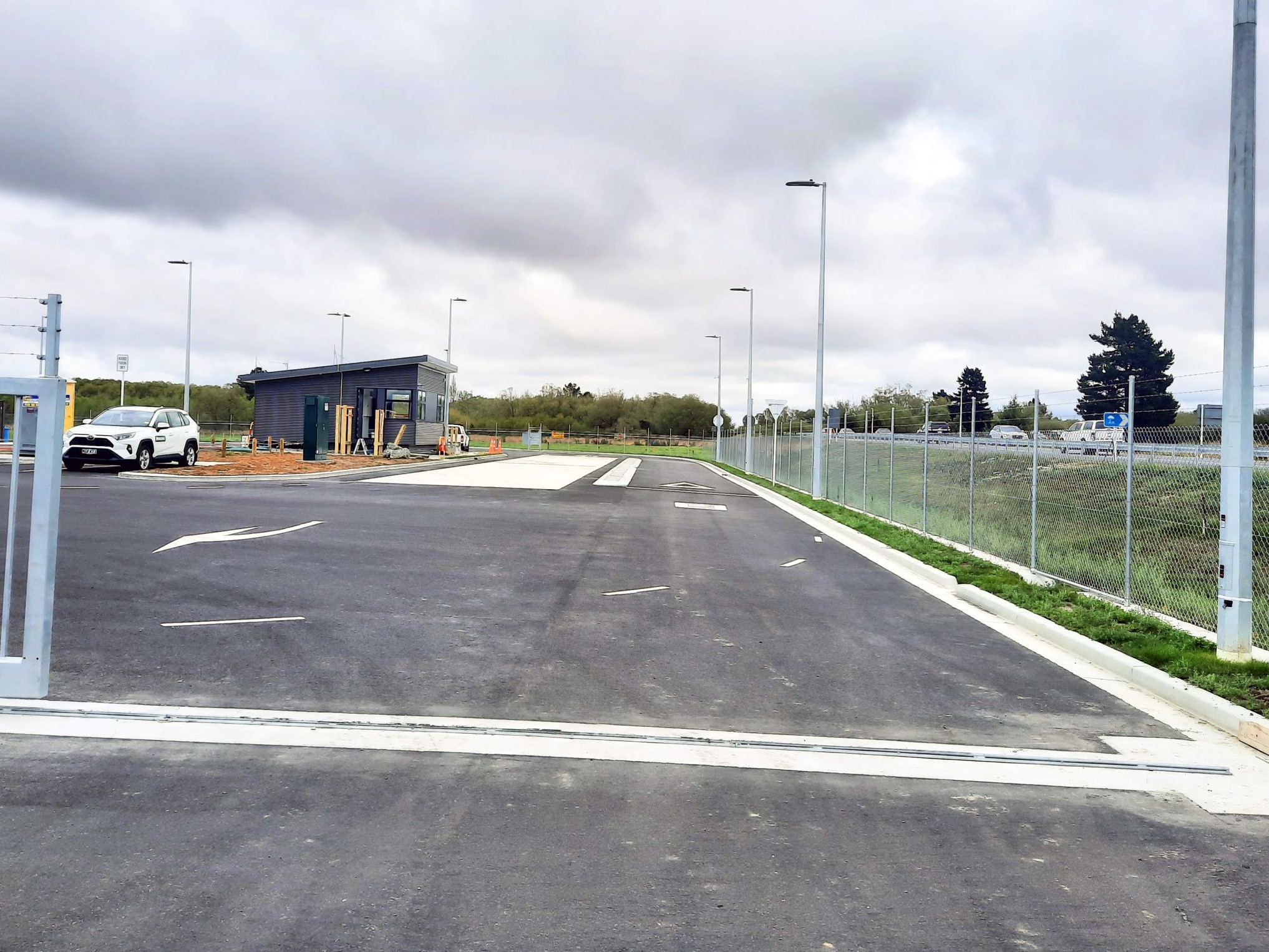
By coincidence both last week and this one have ended with figures coming out that show the value our members bring to the economy. And there was even a leap-year software glitch this week that showed again just how good our industry is at keeping things moving.
Firstly, media interest has been high in regard to the impact on freight as a result of the Brynderwyns highway closure north of Auckland.
We are fully supportive of the closure as the route needs to be made much more resilient. However, when Waka Kotahi announced the detour routes a couple of weeks ago, one of our eagle-eyed members saw the maps were unclear in regard to what trucks were allowed on the proposed detour routes.
Fortunately we were able to fix this before the closure but it was useful to quantitatively establish the financial impact of the closure. The shortest detour route adds an extra 20 minutes to the section that would normally take about 30 minutes. The longer alternative detour, via Dargaville, adds an extra 55 minutes.
Considering the typical daily truck traffic in the region, if all trucks could take the shorter route that equates to adding about $80,000 per day to freight costs. But if all trucks had to take the longer route, that would add about $240,000 per day to freight costs.
When I mentioned those numbers to a journalist there was not only some surprise but I also sensed some disbelief, so I worked through the numbers and they agreed they made sense. I think the reporter was left with a whole new appreciation of the value of freight!
In a similar vein, I ended the week doing a presentation at the ERoad Fleet Day in Christchurch. These are great events and it’s fascinating having both the light and heavy fleet operators sharing their knowledge and learnings.
My presentation was about decarbonising the current heavy fleet and I spent some time at the start increasing awareness on the energy intensity of trucks.
Too often people look at trucks as poor users of fuel, and I’ve seen trucks described as “gross emitters”. But comparing the typical fuel burn and the payloads of a truck and a light utility shows that while a truck burns 8 times more fuel for each kilometre travelled, it carries 181 times more load by weight.
When you look at it that way, I think it a gross misrepresentation, as well as being very unfair, to say that trucks are gross emitters!
During my trip to Christchurch I took the chance to visit a member out towards Mount Hutt, and I also looked at the new Commercial Vehicle Safety Centre under construction for southbound trucks situated just north of the Rakaia River.
We are trying to establish Waka Kotahi’s strategy in regard use of high-speed weigh-in-motion (WIM) systems. From earlier discussions and presentations it appeared that Waka Kotahi’s intent was to automatically invoice trucks from June this year for unpaid road user charges based on the weight measured over the high-speed WIM.
High-speed WIM has been used in a range of countries over the last 25 years or so and I’ve visited sites in South Africa in 2006 and in the US. There have been plenty of concerns about the accuracy of high-speed WIM and these were discussed at the conference I attended in Brisbane last year.
We have been concerned that operators would be considered guilty until they proved themselves innocent if Waka Kotahi forged ahead with a plan to auto invoice operators for unpaid RUC based on the current technology.
However, our latest understanding is that the high-speed WIM will only be used as a screening tool. That would be more aligned with international practice and I think it’s a good move by Waka Kotahi.
We are seeking confirmation from Waka Kotahi on how it will use the high-speed WIM so, as is often the case, watch this space!
Finally, a massive shout out to all our members and their teams that were hit by the disruption to outdoor fuel payment terminals. It appears the extra day in February this year caused a backend software for payments at most, if not all, fuel suppliers.
Media interest on the impact of this on the supply chain was very high. To the best of my knowledge, goods still got to where they needed to get to – supermarkets got their supplies and essentials the public need didn’t run out.
While this was a significant inconvenience to transport businesses and their teams, as usual truckies showed great initiative and resourcefulness to find a work-around to avoid a massive impact on getting goods to where they needed to be.
I think on the one hand reporters were pretty impressed with how our industry responded, but I almost got the feeling they were disappointed there wasn’t a bigger story of supply chain failure!
Our industry’s response was another example of the can-do drive that makes me proud to be a part of it.